Longer, Cleaner Plating Bath Life
Angelo Magrone of Bales Metal Surface Solutions suggests adding an agitation and filtration system to keep plating pretreatment tanks cleaner, longer.
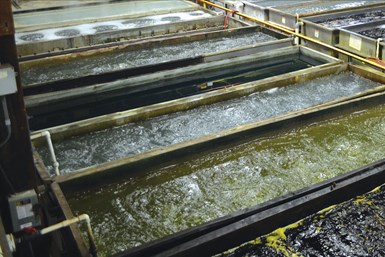
Q: What can I do to ensure a longer, cleaner bath life for plating pretreatment?
Just like our dinner dishes, letting parts soak is a perfectly adequate way of cleaning them before plating. However, what if we can clean them faster, without interrupting the manufactures’ parameters? I think we can all agree on how important pretreatment is to plating. So why do we tolerate letting cleaning solutions get fouled up just to dump them and make a fresh batch? Without clean parts, we can have issues like blisters, poor adhesion, pitting, peeling, or flaking, just to name a few. So, what would happen if we added an agitation and filtration system to our cleaners?
Welcome! You’ve unlocked premium content.
I know what you’re thinking; “Our cleaning solutions don’t cost us that much, why would I spend more money on them?” My response: with the filters removing bulk soils and particulates as they are introduced to the bath, you can ensure a longer, cleaner bath life. With the use of an agitation system, a bath is able to mechanically sweep particulate away from the substrate with fresh chemistry as opposed to letting the cleaner do all the work. This results in reduced heat stratification, allowing a more uniform bath, using less energy.
So, what does this all mean?
Following the manufactures’ recommendations of temperature, pH and concentration of chemistry, the filters have the potential to double the life of the bath. The agitation system has the potential to decrease clean cycle time by up to 20-50%, depending on soil type.
Before using this technology, we were decanting our soap tank every four weeks. This cost us 4.5 hours of labor plus the cost of chemistry replenishment, tank downtime (if your tanks are not full, you’re not making money) and waste treatment per month. Now that we have added agitation and filtration to our cleaning tank, we decant every 12 weeks. Besides the cost savings from reducing all the above, we have compounding savings as well. We now have cleaner parts moving down the line, which causes a direct reduction in rework. We reduced the risk of dragging soil into our rinses and processing tanks. Our rinses stay cleaner for longer (we all know water is not cheap; neither is treating it for waste), which keeps our process tanks cleaner for longer. The technology reduced energy consumption for tank heat-up time by being able to stretch out the time between decanting. The agitation has helped keep our heaters clean from scale buildup, ensuring a longer heater life. We have also saved on haul-away cost as we are now able to reduce the number of pick ups due to not having to “dump and pump” a new tank as often.
Now I ask you, does it make sense to keep your cleaners clean?
Reduction in cycle time, time between decanting and overall cost savings may differ due to tank size, dirt load, and type of equipment used.
Related Content
-
Replacing Open-Top Vapor Degreasing in Aerospace Manufacturing
Options and considerations for cleaning aerospace parts as regulations tighten on vapor degreasing solvents.
-
Solvent Versus Aqueous: Busting the Myths
Is aqueous cleaning “greener” than solvent cleaning? Is solvent a more effective cleaner than aqueous? These and many other questions are answered here to debunk the misconceptions that many manufacturers have held onto for years.
-
Corrosion Resistance Testing for Powder Coating
Salt spray can be useful to help compare different pretreatment methods and coatings but it does not tell us much about the corrosion resistance of a part over time in the field. Powder coating expert Rodger Talbert offers insights into how to get a better idea of how to improve a part’s corrosion resistance in the real world.