NIBORE™
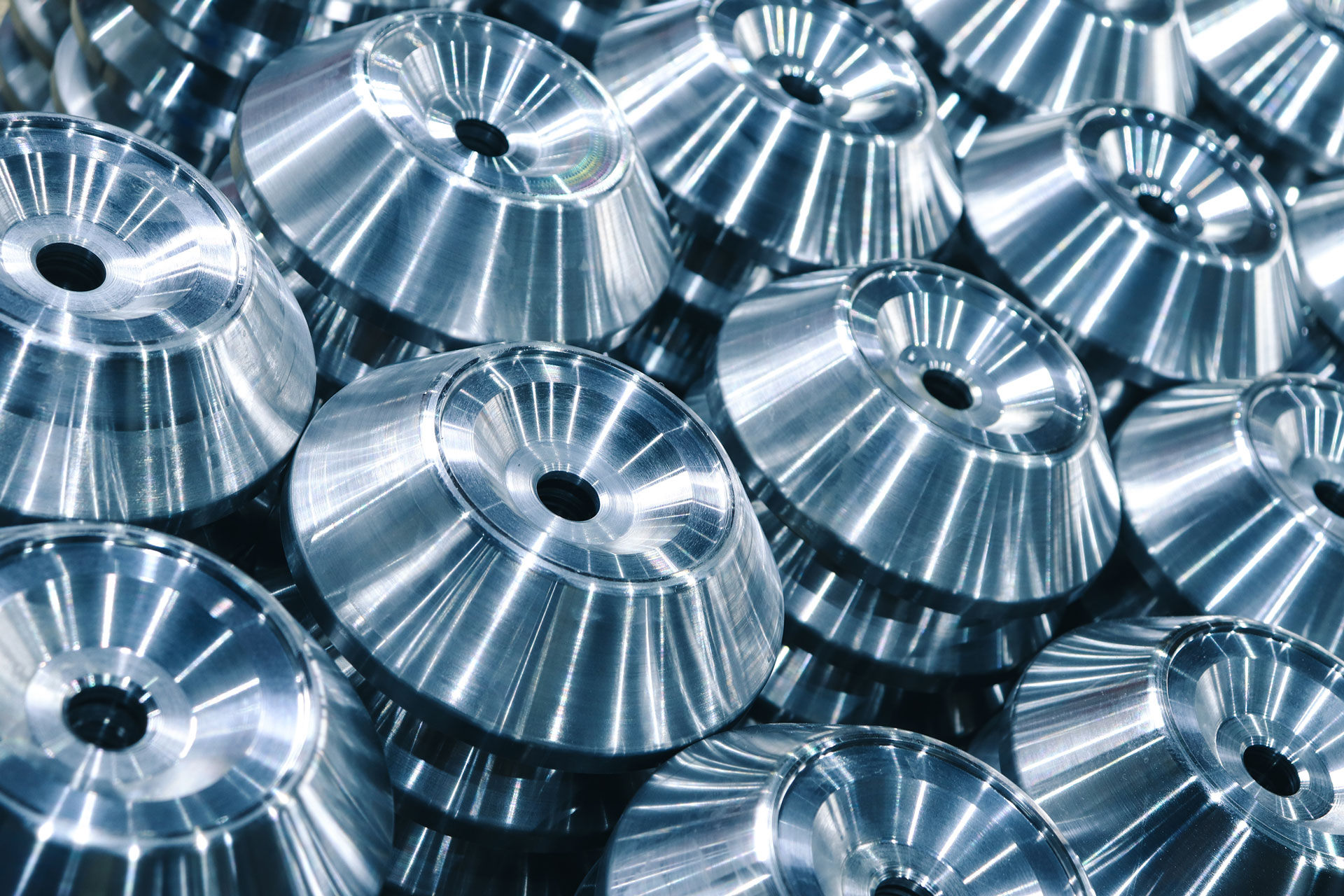
THERE’S A LOT TO LOVE ABOUT NIBORE™
NIBORE™ is a proprietary nickel boron coating that offers a superior level of lubricity and release, an excellent level of abrasion and wear resistance, plus an extremely low coefficient of friction. Electroless plating doesn’t require an electric current; thus, NIBORE™ nickel boron coatings will be even, regardless of the surface.
NIBORE™ combines electroless nickel and boron nitride featuring a high working temperature so you can use it even in extreme applications.
NIBORE™ COATING BENEFITS
Explore the additional benefits of NIBORE™ coating for any application.
- 54 Rockwell hardness rating or 67 Rockwell hardness rating after 550°F (288°C) heat treatment.
- Application of up to a 0.0005” deposit.
- Extremely low coefficient of friction (0.05).
- Withstands up to 1250°F (677°C), well above the 550°F (288°C) range for PTFE coatings.
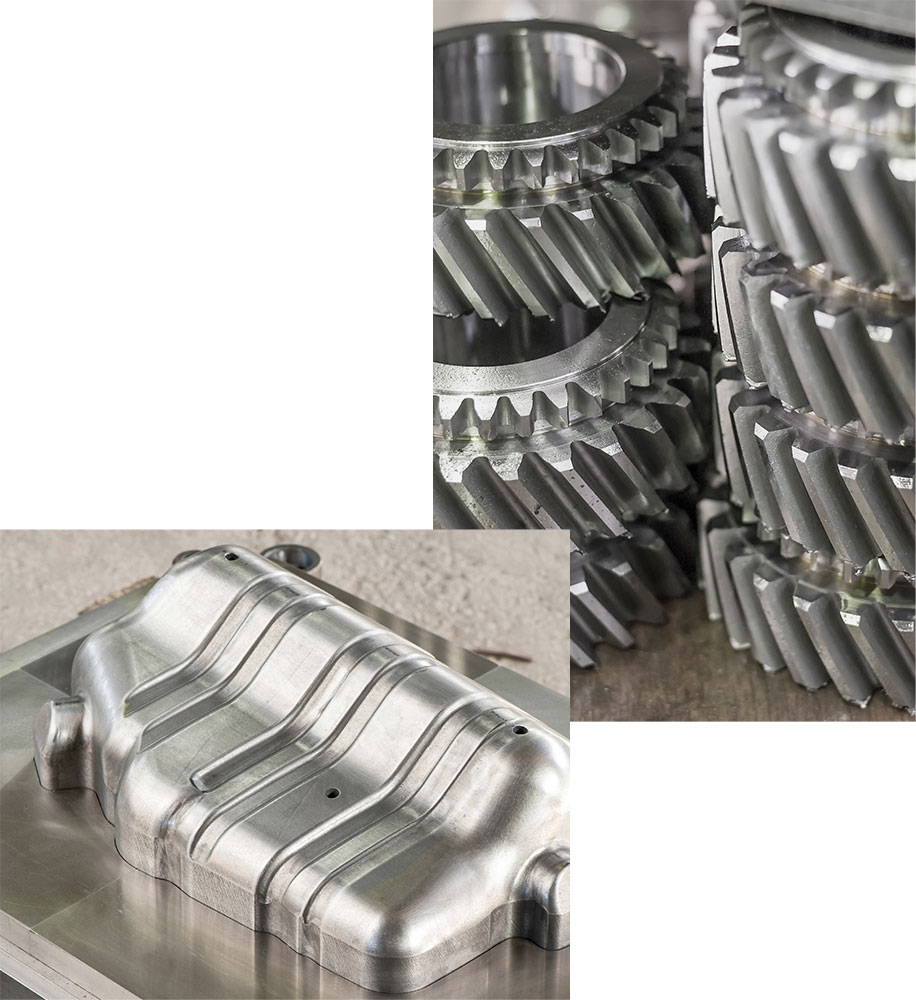
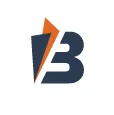
LOW-FRICTION COATINGS
Do you have parts prone to getting rubbed the wrong way? Solve your abrasion and wear problems with our abrasion-resistant coatings.
ABRASION-RESISTANT COATINGS
Are release issues causing downtime in your shop? Reduce friction and achieve uniform treatment with our lubricity and release/low-friction coatings.
NIBORE™ COATING FAQS
NIBORE™ coatings offer exceptional hardness and wear resistance, plus excellent lubricity. They are ideal for applications requiring both durability and release, including consumer products, machined components, and automation & linear motion. Keep reading to discover how these coatings provide lasting metal surface protection.
Does NIBORE™ Wear Off?
NIBORE™ coatings are highly durable and designed for longevity in severe operating conditions. While all coatings can wear over time, especially under extreme friction, stress, or improper maintenance, NIBORE™ is less likely to wear off under normal usage conditions due to its hardness and wear-resistant properties. Regular maintenance and proper application can significantly extend the lifespan of a NIBORE™ coating.
Does NIBORE™ Rust?
NIBORE™ coatings offer excellent corrosion resistance, significantly reducing the risk of rusting on the coated surface. The unique composition of NIBORE™ creates a barrier that protects the underlying metal from oxidation and environmental factors that lead to rust. However, like any protective coating, its effectiveness can be compromised if the coating is damaged or excessively worn, exposing the metal beneath.
How Does a NIBORE™ Coating Work?
A NIBORE™ coating works by depositing a thin layer of NIBORE™ alloy onto the surface of a metal part through an electroless plating process. This coating significantly enhances the surface properties of the treated parts, including hardness, wear resistance, and corrosion resistance. The NIBORE™ layer also reduces friction, which can improve the operation of moving parts. The result is a durable, high-performance surface that extends the life and efficiency of coated components.
Which is Better: NIBORE™ or Chrome?
Choosing between NIBORE™ and Chrome coatings depends on the specific requirements of the application. NIBORE™ is known for its superior hardness, wear resistance, and reduced friction properties, making it ideal for high-stress and precision applications. Chrome, on the other hand, is renowned for its surface hardness. While both coatings are durable, NIBORE™ often provides a better balance of lubricity and durability, making it preferable for applications requiring both performance enhancements.
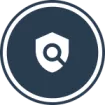
54-67
ROCKWELL HARDNESS
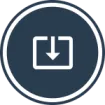
0.05>
COEFFICIENT OF FRICTION
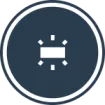
185°F
applied TEMPERATURE
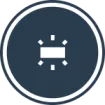
1250°F
MAX OPERATING TEMPERATURE
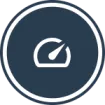
4-6%
Phosphorus (wt)
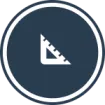
8.1 g/cm3
Density
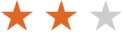
corrosion resistance rating
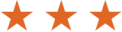
RELEASE RATING
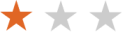
ABRASION resistance rating
CASE STUDY: Nibore™ Solves Beryllium Copper Leaching Problem
A custom plastic injection mold manufacturer tested numerous coatings from different platers, but none stopped its beryllium copper mold from leaching into the product. The story was different once they approached Bales. “Bales’ customer service has been fantastic. They are extremely responsive to our needs, turning things around quickly, whether quotes or the plating process," said Rob Zimmerman, engineering manager at MOS Plastics.
Rob Zimmerman, Engineering Manager at MOS Plastics
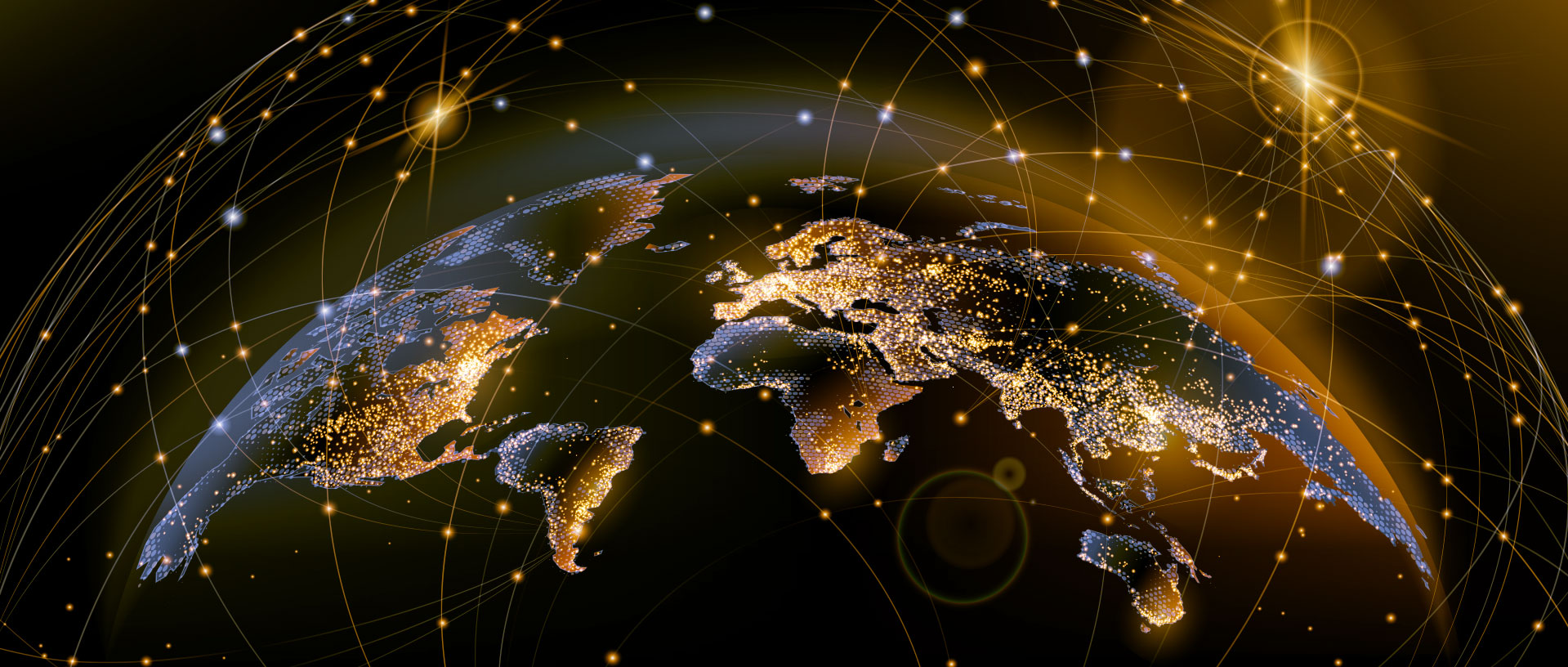